Industrial robots have moved from specialized tools to essential drivers of modern manufacturing. As industries around the world push for greater speed, precision, and adaptability, these robots are no longer optional—they’re foundational. Whether performing high-volume tasks or integrating into smart factory systems, industrial robots now represent a core element of digital transformation in production.
The global demand for industrial robots is growing rapidly as businesses strive for faster, smarter, and more flexible manufacturing. For example, Germany is partnering with companies like NVIDIA to build national AI cloud systems that support next-gen robotics and automation. Meanwhile, Amazon operates over one million robots in its warehouses, including Autonomous Mobile Robots (AMRs) and robotic arms that efficiently sort, pick, and pack products. Even major events like the FIFA Club World Cup use robotics to manage logistics at large scale.
Recent advancements in technologies like machine learning for robotics, industrial internet of things (IIoT), and digital twin in manufacturing have enabled robots to become smarter and more adaptable. Today’s robots not only perform tasks with precision—they can also predict maintenance needs, avoiding costly downtime and improving efficiency.
In this post, we explore what industrial robots are, how they differ from collaborative robots (cobots), and why they’re central to today’s smart manufacturing. You’ll learn about the most common robot types—like articulated, SCARA, and Cartesian robots—the technologies fueling their evolution, and their growing role in global production. From warehouse logistics to precision electronics, we show how industrial robots are reshaping how goods are made, moved, and managed.
What Are Industrial Robots and How Do They Differ from Cobots?
Industrial robots are the backbone of modern smart manufacturing. These programmable machines are designed to perform repetitive, high-precision tasks—such as welding, assembly, and material handling—in environments that are unsafe, inefficient, or physically demanding for humans. Commonly deployed in factory automation, they excel at what are known as the “3D” jobs: dirty, dull, and dangerous. Operating with speed and consistency, these robots help improve safety, reduce labor costs, and boost production efficiency—especially in large-scale, high-volume settings.
Common Types of Industrial Robots:
Articulated robots: These robots have rotary joints and are flexible like a human arm, making them ideal for tasks such as welding or painting.
SCARA robots: Known for their fast, precise movements in horizontal planes, SCARA robots are used primarily in pick-and-place jobs.
Cartesian robots: These robots move along straight lines, offering precision for tasks like 3D printing or CNC machining.
Industrial robots are mainly used for tasks that require precision and repetition—like assembling parts on a production line or welding metal pieces together. They are optimized for tasks where humans would face risks, fatigue, or inefficiency, and they do not typically interact with humans directly.
What About Cobots?
On the other hand, cobots (collaborative robots) are designed to work alongside humans. Unlike industrial robots that often operate in isolation, cobots are built with safety features, such as force sensors and speed limiters, which allow them to share workspaces with humans. Cobots are more flexible and easier to program, making them ideal for smaller-scale tasks or environments where human workers might need assistance with light assembly, product testing, or packaging.
Cobots are a growing segment in robotics automation, offering businesses a cost-effective way to enhance productivity without requiring major changes to existing workflows. Unlike traditional robots, cobots are collaborative, meaning they assist human workers by taking over physically demanding or repetitive tasks, allowing workers to focus on higher-value activities.
Why Is Industrial Robotics Gaining Momentum Around the World?
Industrial robots—whether working independently or alongside humans as cobots—are no longer niche tools. They’ve become foundational to modern manufacturing strategies, offering the speed, precision, and consistency needed in today’s fast-paced industrial environments. As industries look beyond isolated automation toward fully connected, intelligent systems, the adoption of robotics is accelerating worldwide. That momentum isn’t just about efficiency—it’s about staying relevant in an increasingly competitive global market.
Global Manufacturing Is Under Pressure
Manufacturers today face a series of challenges: rising operational complexity, supply chain instability, and demand for mass customization. To stay competitive, they need solutions that can scale quickly, deliver with precision, and adapt in real time. Industrial robots fit the bill—especially as they become smarter through integration with AI, IIoT, and machine learning.
Across North America, Asia, and Europe, governments and private sectors alike are treating robotics automation as a pillar of economic growth. From national AI strategies to regional smart factory initiatives, there’s a clear global shift toward industrial automation as a foundation for innovation.
A Broader Range of Applications
What’s driving the momentum isn’t just the robots themselves—but where and how they’re being used. While traditional use cases like automotive manufacturing still lead in volume, new sectors are ramping up adoption:
Logistics: Autonomous Mobile Robots (AMRs) are streamlining warehouse operations with flexible navigation and smart inventory management.
Electronics: Compact SCARA robots are ideal for assembling delicate components at high speed and accuracy.
Pharmaceuticals and food processing: Robots ensure cleanliness, consistency, and compliance in highly regulated environments.
As AI in robotics improves, these machines aren’t just repeating motions—they’re analyzing data, making adjustments, and learning from operations. That means better quality, less downtime, and higher throughput across more industries.
Robotics as Infrastructure
Industrial robots are no longer seen as standalone tools—they’re becoming part of a company’s infrastructure. Just like power and internet, robotics now underpins critical systems. As predictive maintenance with AI reduces unplanned outages and digital twin in manufacturing allows for smarter planning, companies are seeing automation not as a one-time investment, but as an ongoing competitive asset. Even small and mid-sized businesses are embracing robotics thanks to greater affordability, modular designs, and cloud-based platforms that lower the barrier to entry.
The rise of industrial robotics reflects a broader truth: success in modern manufacturing depends on adaptability, not just output. Robots that can learn, communicate, and evolve are no longer optional—they’re essential for meeting the pace and complexity of global markets.
How Are Industrial Robots Evolving with AI and Smart Technologies?
The global push for robotics automation is no longer just about cutting costs or increasing speed—it's about building smarter, more adaptable manufacturing systems. As businesses face pressure to stay agile in a fast-changing world, industrial robots are becoming strategic assets that drive innovation, flexibility, and resilience. But this transformation isn't just about adding more robots—it's about making them smarter. This shift is driven by advances in AI in robotics, machine learning, and the rise of smart manufacturing technologies.
Smarter, Not Just Stronger
Traditional industrial robots were excellent at one thing: doing the same job over and over again with precision. But modern manufacturing demands more flexibility. Product designs change quickly, production lines need reconfiguration, and small-batch customization is becoming the norm.
Now, with machine learning for robotics, robots can learn from data, recognize patterns, and adjust their behavior without reprogramming. For example, a robot assembling electronics might now detect a misaligned component and reposition it on the fly—something older robots could never do without stopping the line.
This evolution is made possible by several key technologies:
Computer vision: allows robots to interpret their environment visually.
Sensor fusion: combines input from cameras, force sensors, and motion detectors for real-time decisions.
Predictive maintenance with AI: monitors internal systems to detect early signs of failure and prevent unplanned downtime.
Connected Systems and Digital Twins
These smarter robots don’t work in isolation. Thanks to the Industrial Internet of Things (IIoT), they’re part of a fully connected ecosystem where machines, sensors, software, and cloud platforms continuously exchange data. This real-time connectivity allows every robot, from a single robotic arm on the floor to an entire fleet of autonomous mobile robots (AMRs), to function as part of a synchronized, data-driven system. Instead of working alone on fixed tasks, each robot can adjust its behavior based on feedback from surrounding equipment, environmental sensors, or changes in production schedules.
That constant stream of data also powers the digital twin in manufacturing—a powerful tool that creates real-time, virtual replicas of physical production lines, equipment, or even entire facilities. A digital twin allows engineers and plant managers to simulate changes, test new production scenarios, or troubleshoot problems before making adjustments in the real world.
Over time, the digital twin evolves alongside the real system, incorporating live performance data and learning from it. This makes it possible to predict outcomes more accurately, detect inefficiencies, and drive continuous improvement. In global operations, digital twins also make it easier to replicate success across multiple sites—ensuring consistency and efficiency at scale.
Real-World Example: ABB at Automatica 2025
ABB is already leading this transformation. At the Automatica 2025 expo, it introduced a new generation of heavy-duty industrial robots and autonomous mobile robots (AMRs) designed not only for power and precision but also for adaptability. These machines communicate with cloud platforms, adjust to production shifts, and deliver detailed performance analytics—bridging the gap between robotics automation and strategic factory intelligence.
This isn’t just a technical upgrade—it’s a competitive advantage. Smarter robots mean fewer breakdowns, faster changeovers, and more responsive supply chains. For manufacturers competing on speed, quality, and customization, adopting intelligent robotics isn’t just helpful—it’s essential for long-term growth and resilience.
Will Robots Replace Humans?
While industrial robots are transforming manufacturing with greater speed, precision, and intelligence, their impact goes far beyond the factory floor. As automation expands, it reshapes not just how things are made—but also who makes them, and what kinds of jobs remain. To understand this shift, it’s essential to look at how robotics is affecting employment. Research on the employment impact of industrial robots draws on several key studies, most notably Robots and Jobs: Evidence from US Labor Markets, The Effects of Industrial Robots on Employment and Automation and New Tasks: How Technology Displaces and Reinstates Labor. Together, these studies offer a nuanced picture of how automation affects the workforce—highlighting long-term job displacement, demographic disparities, and shifting wage dynamics.
1. Job Losses Are Real—But Unevenly Distributed
Industrial robots primarily replace routine, manual labor—making their impact especially hard on certain groups. Between 1993 and 2014, research shows:
Employment among men declined by 3.7%, compared to 1.6% for women
Non-white workers saw a 4.5% drop in employment, versus 1.8% among white workers
These gaps reflect the concentration of men and minority workers in manufacturing and logistics roles, where robots are most widely deployed. And the effects ripple outward—when factory jobs vanish, nearby service jobs often disappear as well.
2. Long-Term Displacement with Fewer New Jobs
Over the past few decades, automation has steadily reduced the number of low- and middle-skill jobs in industries like manufacturing. Yet the economy has struggled to generate enough new roles to absorb displaced workers. While automation boosts productivity at the firm level, it hasn’t reliably produced new employment opportunities of similar quality, especially for lower-skilled workers.
3. Productivity Gains Don’t Always Mean Employment Gains
Firms that invest in robotics often do grow and add jobs—largely because they outperform competitors. But across an entire industry, these gains rarely make up for the losses. As leading firms scale up with automation, smaller or slower adopters tend to shed jobs or shut down. The result is uneven progress: localized growth, but broader disruption.
4.Wages and Job Quality Are Also Affected
Even when jobs aren’t eliminated, they may still be reshaped. Automation has been linked to slower wage growth, especially for mid-skill workers whose tasks are partially automated. In Europe, increased robot adoption has also been associated with higher work intensity and declining job satisfaction. In short, robots don’t just change who does the work—but also how that work is experienced.
Who Are the Key Players in Industrial Robotics?
As industrial robots reshape the workforce and redefine factory operations, they’re also driving a massive shift in the global economy. Behind this transformation are some of the world’s most influential companies—pioneers not only in building robots, but in developing the intelligent systems that power them. From hardware innovation to AI-driven cloud platforms, these key players are shaping the future of manufacturing at scale.
ABB: Headquartered in Switzerland, ABB is a global leader in industrial automation. Its lineup includes robotic arms, mobile robots, and customized solutions for factory automation, logistics, electronics, and automotive sectors. ABB is also investing in digital twin in manufacturing and predictive maintenance with AI through its connected platforms.
FANUC: This Japanese company is one of the most recognized names in industrial robot manufacturing. FANUC’s R-2000iB robot is widely used in welding, handling, and assembly operations, prized for speed and durability.
KUKA: Based in Germany, KUKA specializes in intelligent robotics automation and cobots. Their robots are found in aerospace, automotive, and metal industries. KUKA is also expanding its software capabilities for smart factory management.
Yaskawa: Known for high-precision motion control and welding automation, Yaskawa’s industrial robots are staples in factories worldwide. Their focus includes SCARA robots and high-speed robotic arms for electronics and automotive applications.
Amazon: With over 1 million robots deployed globally, Amazon is transforming logistics and fulfillment through robotics. Its systems are no longer just about automation—they now use AI foundation models to predict and adapt in real time.
WhalesBot: As a rising force in educational and applied robotics, WhalesBot bridges the gap between industrial robotics and hands-on learning. WhalesBot deploys the EnginBot to build its own automotive production line for simulated tasks like welding, assembly, and inspection. These aren’t just demo models—they show real-world applications of robotics automation in a scaled-down, accessible format.
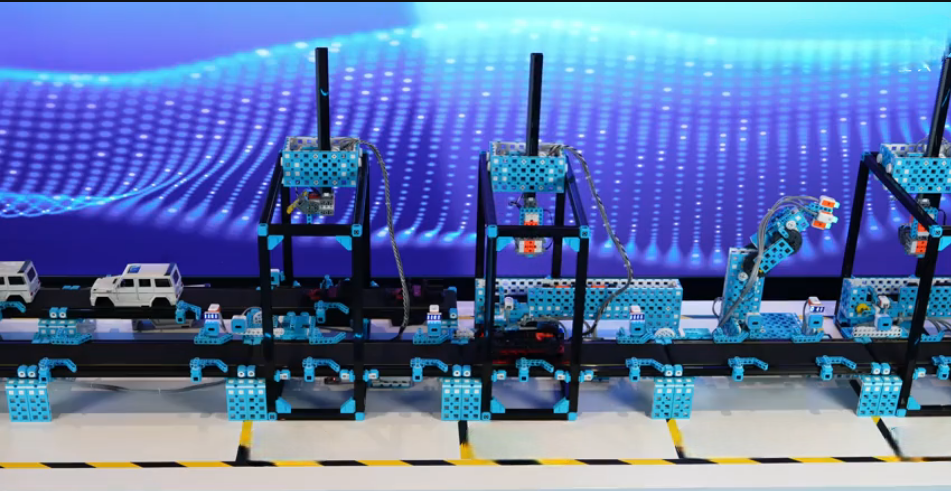
Want to let your child experience the excitement of automation firsthand? WhalesBot offers interactive, child-friendly production lines where students can simulate factory operations at home or in our showroom. Try building your own smart factory and explore robotics up close. Chat with us or book a visit at our official website https://www.whalesbot.ai/.
Final Thoughts: What’s Next for Industrial Robots?
Industrial robots are no longer just mechanical arms bolted to factory floors. They’re evolving into intelligent systems—powered by AI, connected through the industrial internet of things, and increasingly capable of working side-by-side with humans through cobots. From the warehouse robots at Amazon to Germany’s push for AI-driven production, one thing is clear: smart manufacturing is becoming the norm, not the exception. And industrial robots are at the center of that transformation.
We’ve moved past the era of robots doing just the dirty, dull, and dangerous jobs. With machine learning for robotics, predictive analytics, and digital twins in manufacturing, robots are now decision-makers, problem-solvers, and—at times—collaborators. The future of industrial robotics lies in greater autonomy, flexibility, and intelligence. With advances in machine learning for robotics, robots will move beyond following rules—they’ll start learning from their environments and adapting in real time. We’ll see more robots making decisions, adjusting to production changes on the fly, and even collaborating across global factories through cloud platforms and digital twins. So if you're curious about how robotics can transform your workflow, your factory, or your future—this is the time to dig deeper!